What are Refractory Precast Shapes? Refractory Precast Shapes are refractory components that are baked or cured after on-site construction. It is a commonly used building material for high-temperature equipment. Refractory precast offers superior performance and better quality control than traditional on-site masonry. Usually, Refractory Precast Shapes are cast or pressed on-site, then dried or sintered and solidified in the factory, and then transported to the site for installation.
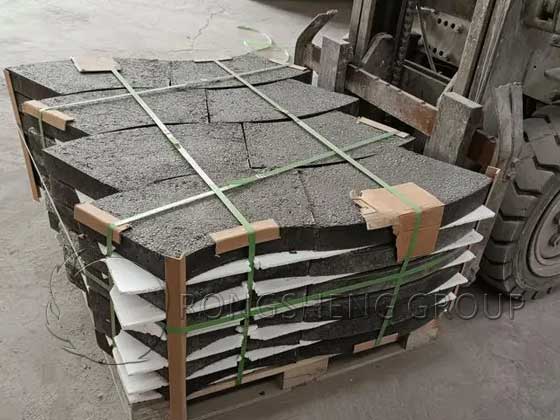
There are many types of Refractory Precast Shapes. According to different uses, it can be divided into various types such as high-temperature resistance, acid and alkali corrosion resistance, wear resistance, etc. Among them, Refractory Precast Shapes with high-temperature resistance are the most widely used. For example, tunnel kilns, oil refineries, metallurgical industries, glass industries, power industries, etc. all need to use Refractory Precast Shapes for thermal insulation.
Common Refractory Precast Shapes include refractory bricks, refractory panels, refractory balls, etc. Different precast shapes come in different shapes and sizes and can be selected according to different needs. They have good heat insulation, wear resistance, corrosion resistance, and other characteristics in high-temperature environments. It can effectively protect equipment, extend equipment service life, and reduce equipment maintenance costs.
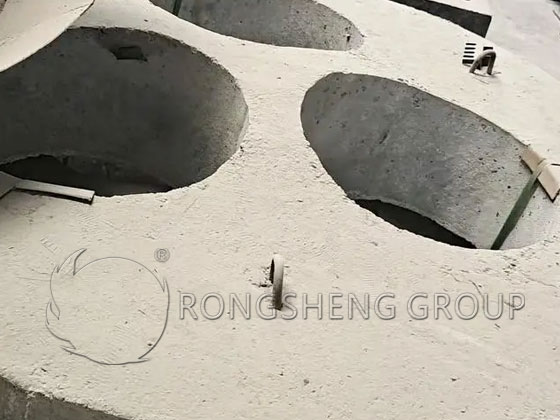
Advantages and Disadvantages of Using Refractory Precast Shapes
With the continuous development of unshaped refractory castables, Refractory Precast Shapes are becoming more diverse and larger in proportion. However, using Refractory Precast Shapes also has certain advantages and disadvantages.
Advantages of Precast. Because it is made into different shapes according to the size specifications of special parts of the furnace, the construction is convenient and quick when in use. And the oven time is short. Because there are many manufacturers that bake drains at a certain temperature after producing them, so they can heat up quickly.
In addition, precast shapes have good thermal insulation properties. Because it is precasted and molded according to the shape of the parts, there are no gaps, good heat insulation effect, and strong air tightness. Refractory Precast Shapes are made of different materials. However, baked preforms have good creep properties and strong wear resistance.
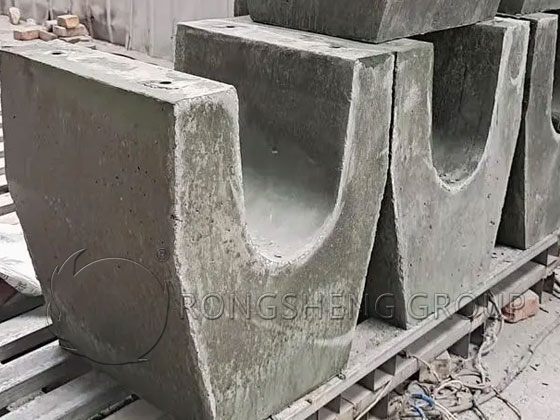
Disadvantages of prefabs. The added high-alumina cement has a large binder dose, high calcium content, and strong density, and at the same time, bad thermal shock may occur. High calcium content and many impurities will also reduce the refractoriness of precast shapes. Moreover, some manufacturers do not use low and medium-temperature barbecues during the production process, and the crystal water is not fully discharged at all. It is extremely easy to explode during use. Some even crack when reaching a certain high-temperature area during use, making the Refractory Precast Shapes no longer usable.
Many manufacturers will add a certain proportion of explosion-proof fiber in the process of producing Refractory Precast Shapes. However, the drainage process is short, and the crystal water is not fully discharged before being transported and used. Then during the transportation process, explosions have already occurred.
Some precast shapes seem to take a long time to drain, but unbaked Refractory Precast Shapes will shrink after passing a certain temperature during use. Resulting in some changes in the size of the used part.
In short, the production of Refractory Precast Shapes still requires barbecue at a certain temperature. The most reliable method is to fully discharge free water and crystal water.
RS Kiln Refractory Factory is a powerful manufacturer and seller of refractory materials. Our refractory material factory specializes in the production of Refractory Precast Shapes. We strive to provide long-life refractory materials for the refractory linings of high-temperature industrial kilns!