In order to ensure smooth construction and normal use at high temperatures, refractory plastics should generally have the following basic properties. ① Have a certain plasticity to facilitate construction. ② Have a certain storage period to ensure that the molding performance remains unchanged during the specified storage period. ③ After curing at room temperature, it will have a certain strength, so that the frame can be dismantled or transported after construction. ④ Have certain high-temperature volume stability to prevent damage to the furnace lining structure due to excessive deformation. The reason why refractory plastic is called refractory plastic, is what does its plasticity have to do with it?
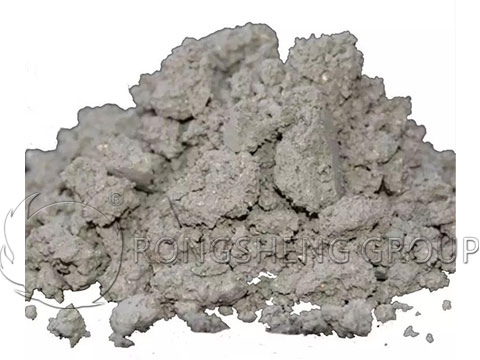
Why is Refractory Plastic with Plasticity?
The plasticity of the plastic has a direct impact on the characteristics and dosage of the clay. It is also related to the amount of water added. Plasticity increases as the amount of water added increases. But it cannot be too high, generally 5~10%. Improving plasticity means controlling the amount of clay and water in the plastic, and adding plasticizers.
The role of plasticizers in refractory plastics. ① Improve the hygroscopicity of clay particles so that the clay particles are dispersed and coated with a water film. ② Solve the clay particles. ③ Increase the electrostatic repulsion between clay particles and stabilize the sol. ④ Exclude ions that hinder solization from the system as insoluble salts. ⑤ Increase the viscosity of the water in the clay to form a strong water film, etc. Commonly used plasticizers mainly include pulp waste liquid, naphthenic acid, lignosulfonate, lignophosphate, lignochromate, etc. At the same time, the binders used in refractory plastics also have a certain impact on plasticity.
Soft clay is an important raw material for refractory plastics, and the main performance characteristics of plastics are also derived from soft clay. In refractory plastics, soft clay not only functions as a binder but also as a plasticizer and sintering agent. It has a great influence on the plasticity, water retention, construction ability, normal temperature, and high-temperature fire resistance of refractory plastics. Therefore, the soft clay used to prepare fire-resistant plastics should have good plasticity, hygroscopicity, moderate viscosity, fire resistance, and sintering properties. Its fineness: less than 0.09mm accounts for more than 85%, and the dosage is 10%~15%.
The chemical binding agent is an aluminum sulfate solution with a density of 1.2~1.3g/cm³. After mixing with this binder, the material should be trapped for more than 16 hours. Because the sulfate radical in aluminum sulfate reacts with the iron in the powder, iron sulfate is generated and hydrogen gas is released. This will cause the mud to bubble or bulge, so the material should be trapped.
Refractory plastic is a high-temperature material that is usually composed of a variety of raw materials. The specific proportions and material types of its formula can vary depending on different manufacturers, products, and application environments of refractory plastic. Below are some common components of a typical refractory plastic formulation.
- Aluminum silicate can be used in plastic formulations. Aluminum silicate fiber, adhesive, filler (such as clay, expanded perlite, etc.), modified resin, etc.
- High aluminum plastic formula. High-aluminum raw materials (such as high alumina, alumina, etc.), binders (such as phosphates, sulfates, etc.), fillers (such as calcium carbonate, wollastonite, etc.), etc.
- Zirconia can be used in plastic formulations. Zirconia powder, binders (such as silicate, borate, etc.), reinforcing agents, fillers, etc.
- Silicon carbide can be used in plastic formulations. Silicon carbide powder, organic binders (such as resin, asphalt, etc.), fillers (such as kaolin, talc powder, etc.), etc.
- Aluminum borate can be used in plastic formulations. Aluminum borate fiber, fillers (such as kaolin, talc, etc.), binders (such as expanded mica, etc.), modified resin, etc.
- Aluminum phosphate can be used in plastic formulations. Aluminum phosphate fiber, clay, adhesive, reinforcing agent, anti-slump agent, etc.
It should be noted that the above are only typical components in some common refractory plastic formulas. The specific formula proportions and types may vary depending on the manufacturer and product type. When using refractory plastics, preparation and construction should be carried out in strict accordance with the product instructions and technical parameter requirements.