The cement kiln is divided into two major systems: preheater and rotary kiln. The preheater system is generally a five-stage air duct, and the rotary kiln system is divided into a front transition zone, a firing zone, and a cooling zone.
With the continuous improvement and improvement of castable technology, the amount of castables used in cement kilns is also increasing. The cyclone cylinder uses alkali-resistant bricks, and many manufacturers use alkali-resistant castables instead. The kiln tail preheating system of dry-process cement kilns also uses alkali-resistant castables. The properties of alkali-resistant castables are divided into ordinary alkali-resistant castables and high-strength alkali-resistant castables. Generally speaking, ordinary alkali-resistant castables are bonded with ordinary cement, while high-strength alkali-resistant castables are bonded with low cement.
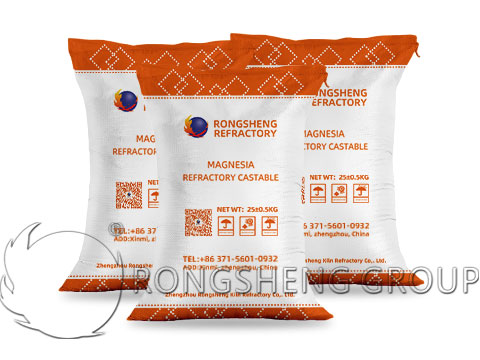
Refractory castables for cement kiln preheating system
It is more suitable to use alkali-resistant castables for the preheating system. In the decomposition zone at the end of the cement kiln, low cement wear-resistant castables should be used.
In the cone of the preheater, the discharge pipe, and the parts at the end of the kiln that are prone to crusting, anti-crushing castables are used.
The alkali-resistant insulating castables used at the end of the kiln are now basically made of calcium silicate boards. As a castable manufacturer, we do not recommend the use of insulating castables because of their high density and poor wear resistance as calcium boards. It is also inconvenient to set up molds. Therefore, for the sake of users, it is still a good choice to use calcium silicate boards for heat insulation parts.
Refractory castables for cement kiln rotary kiln system
In the rotary kiln system, magnesia series bricks are used. The only parts where castables are used are the kiln mouth and coal injection pipe. The castable requirements for coal injection pipes are relatively high-end because this part is highly corrosive. Some use silicon carbide castables, some use magnesia-aluminum spinel castables, and some use corundum mullite castables. But no matter which type is used, the density of coal injection pipe castables is generally around 2.9. In addition, the compressive strength is greater than 100 Mpa, because the use conditions of this part are quite harsh.
In general, cement kilns should use high-aluminum refractory castables for kiln door covers. The grate cooler uses high-strength alkali-resistant castables, and wear-resistant castables should be used in parts of the grate cooler that are prone to wear.
Wear-resistant castables can also be used at the rear entrance of the cement kiln, but they must be alkali-resistant. Steel fiber reinforced refractory castables are also available. The front kiln mouth is also a relatively demanding part. It uses high-end castable corundum mullite castable, but it must have wear resistance. But the dosage is not very large, usually 8-10 tons.
For the decomposition furnace at the end of the kiln, low-cement castables must be used, the alkali resistance must be level two or above, and the aluminum content must not be less than 70%. However, alkali-resistant castables must be used at the cone, and alkali-resistant castables can also be used at the top. The strength requirement of alkali-resistant castables cannot be less than 60Mpa.
There are also coal-injection pipes. Although the amount is not large, the requirements are extremely demanding. Corundum-mullite castables are used, high-grade castables containing silicon carbide can also be used, and magnesium-aluminum spinel castables are also used.
The tertiary air duct must use wear-resistant castables with a strength of 100Mpa. High-aluminum and low-cement castables are also used for parts with light wear, and the bulk density requirement is 2.6.
There is also a mix of steel fiber castables and wear-resistant bricks used in the single-cylinder cooler mixing zone.
To purchase high-quality refractory castables for cement kilns and to learn about construction issues of refractory castables for cement kilns, please contact us. We can provide high-quality refractory castable products and cost-effective refractory lining design services.