With the continuous development of surface treatment processes in the manufacturing industry, volatile organic compounds are increasingly used in industry. The configuration of regenerative exhaust gas incinerators is becoming more and more urgent. Most volatile organic compounds (VOCs) have special odors, can cause various discomforts to the human body, and are toxic, irritating, and carcinogenic. Under sunlight, photochemical reactions occur between nitrogen oxides, hydrocarbon organic compounds, and oxidants in the atmosphere. Generate photochemical smog, endanger human health and crop growth, and destroy the ozone layer. In recent years, people’s awareness of environmental protection has continued to increase, and their requirements for controlling air pollution have increased. The economical and effective treatment of waste gas containing volatile organic compounds has become an urgent problem that needs to be solved. Then the question arises, how do we complete this waste gas treatment process?
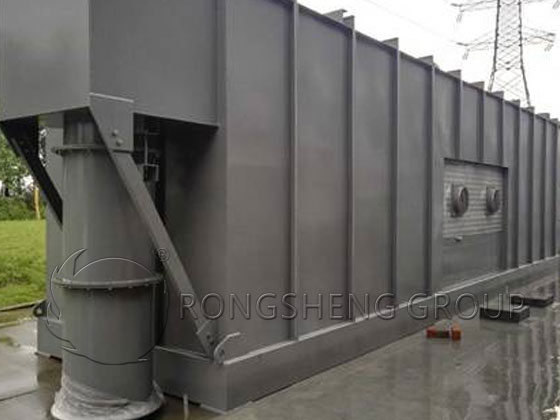
Waste gas treatment of RTO regenerative organic waste gas incinerator
The burned organic waste gas undergoes a thermal oxidation reaction at 760℃~1000℃ to generate carbon dioxide and water. If the organic matter contains other elements such as halogen, the oxidation products will also include hydrogen halide, etc. The exhaust gas is first heated by the regenerator to a temperature close to the thermal oxidation temperature and then enters the combustion chamber for thermal oxidation. The temperature of the oxidized gas increases. The organic matter is essentially converted into carbon dioxide and water. The purified gas passes through another heat storage body, the temperature drops, and can be discharged after reaching the emission standard. Different heat storage bodies are switched over time through switching valves or rotating devices to absorb and release heat respectively.
Seeing the above intuitive analysis, the answer appears. RTO regenerative organic waste gas incinerator can complete the waste gas treatment process.
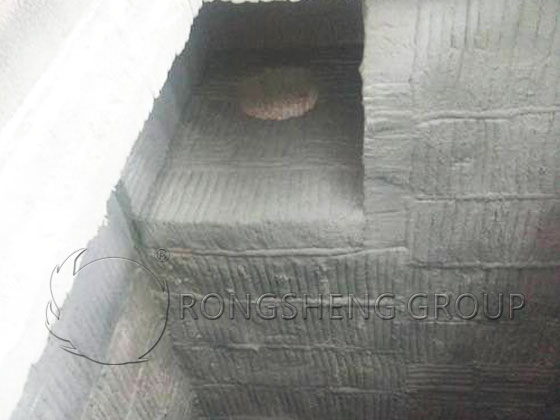
Configuration of insulation materials for RTO regenerative organic waste gas incinerator
The operating temperature of the RTO regenerative organic waste gas incinerator is around 1000°C. In response to the national call for energy conservation, the thermal insulation material in the furnace was originally designed to use ceramic fiber modules with low thermal conductivity and low bulk density as the furnace lining. The traditional dense refractory bricks are abandoned.
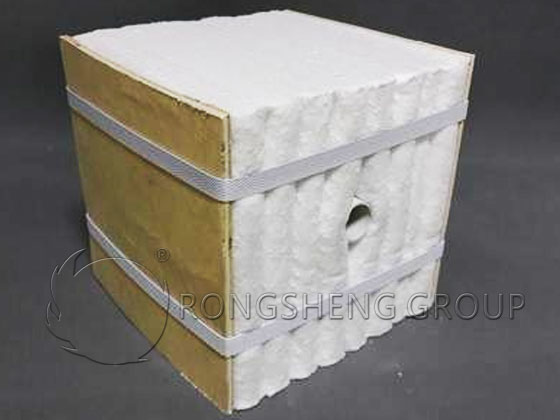
Why choose ceramic fiber modules as the lining when designing the lining of the RTO regenerative incinerator? What are its advantages over duty refractory bricks?
The RTO furnace lining uses a ceramic fiber insulation structure, which can save about 60% of energy compared to brick furnaces according to theoretical calculations. The ceramic fiber module uses high-quality long fiber needle-punched blankets as raw materials, which can achieve rapid heating and high-precision temperature control. Get rid of the disadvantages of dense materials and no need for an oven. This is due to the excellent chemical and thermal stability of the high-quality long-fiber needle-punched blanket used for compressed ceramic fiber modules. Able to resist the effects of rapid cooling and heating on the product itself. The low heat capacity and low thermal conductivity of ceramic fiber modules prevent the module itself from collecting too much heat. It can better distribute heat evenly inside the furnace body. The overall energy-saving effect of the RTO regenerative organic waste gas incinerator is improved.
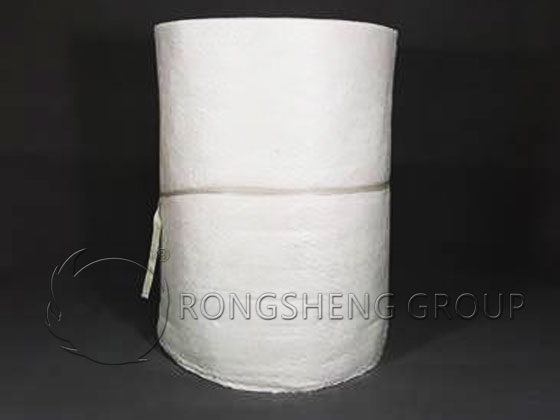
Rongsheng refractory material manufacturer can provide refractory materials for RTO furnace regenerative exhaust gas incinerator insulation engineering. And we already have multiple delivered RTO furnace projects. During the construction process of the full-fiber structure of the RTO regenerative organic waste gas incinerator, staggered joint splicing is used to fix it, forming a seamless overall sealed structure. The energy-saving effect of the stove in use is even more superior.