In the 400,000t steel rolling renovation project of a company, the heating furnace adopts a high-efficiency regenerative full blast furnace gas heating furnace. The furnace organically integrates the high-efficiency regenerative combustion system, the reversing system, and the furnace, and the air and gas are both preheated to 1000°C. The effective length of the furnace is 30m, the width of the furnace body is 4.3m, and the normal heating capacity is 70t/h.
The furnace is a two-stage furnace type with two arch heating sections, heating, and soaking sections. The soaking section is close to the tapping side and a solid furnace bottom soaking bed is set. The rear part of the soaking section and the heating section use upper and lower sides for heating. Except for the furnace bottom, part of the sidewall, and the heat storage type, the whole furnace is made of bricks. The sidewall working layer and the furnace roof are all cast on-site, sharing nearly 1,000t of refractory materials. Among them, the sidewalls and roof of the key parts of the heating furnace adopt low cement castables specially developed for regenerative heating furnaces.
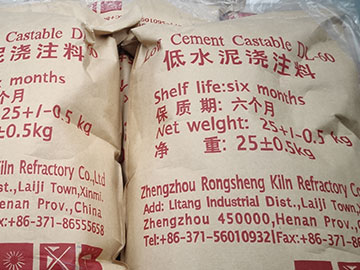
Technical Characteristics of Regenerator Heating Furnace
Compared with conventional heating furnaces, high-efficiency regenerative heating furnaces have the following characteristics:
(1) The burner used in the traditional heating furnace is eliminated and replaced with a nozzle hole composed of refractory castables.
(2) The brick chimney with a height of 40-50m for the traditional heating furnace is eliminated and replaced by a steel chimney with a height of only 18m.
(3) The huge air preheater and gas preheater of the conventional heating furnace are eliminated and replaced by two sets of reversing systems and simpler pipelines, air and gas double preheating. The preheating temperature reaches above 1000°C.
(4) The biggest feature of the regenerative heating furnace is that the furnace wall is hollow. Heated on both sides and equipped with a fire vent, the use conditions are harsh.
The Structural Characteristics of the Sidewall of the Regenerator Heating Furnace
The working principle of the regenerative heating furnace determines that the sidewall has the following characteristics:
(1) For hollow walls, it is relatively difficult to install anchor bricks.
(2) The working surface of the hollow wall is heated on both sides, and the inner wall is easily damaged by the dual effects of temperature changes and airflow.
(3) The flame nozzle of the burner and the working layer are combined into one, which affects the service life of the furnace wall.
(4) Since the air gas has been preheated to 1000℃, it is required that the hollow furnace wall should not have large cracks. Air, gas can not be cascaded.
Refractory Requirements for Regenerator Heating Furnace
The intricate structure of the regenerative heating furnace imposes very strict requirements on the selection of refractory materials:
(1) The high-temperature strength of refractories should be large. It must be able to resist the erosion and corrosion of high-temperature airflow and flame during use.
(2) The refractory materials used must have good thermal shock resistance and can withstand frequent temperature fluctuations without cracking or peeling.
(3) Good volume stability, low linear change rate, and high compressive strength. The cavity between the furnace body is not easy to collapse, and no cracks will occur after long-term high-temperature action. Avoid cracks between the air and gas channels and cause explosion accidents.
(4) With slight expansion. The selected refractory material has micro-expansion during use and prevents cracks.
(5) Good sintering performance. During the use process at 1000~1350℃, it should be ensured that the working layer of the wall can be sintered to form a whole to adapt to the working conditions of heating on both sides.
(6) Good construction performance. When the furnace body is constructed, a large number of special-shaped modules need to be installed. The local gap is extremely small, and in some places it is impossible to complete the building, so the refractory materials must have good construction performance.
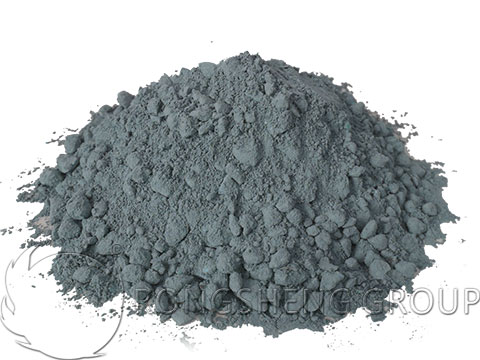
Characteristics of Refractory Materials Selected for Regenerator Heating Furnace
According to the operating conditions of the regenerative heating furnace, the characteristics of the low cement castable used are as follows.
(1) Good thermal shock resistance
The castable has an Al2O3 content of 55% to 67%, and the compressive strength after drying and firing at 1400°C is 15-30MPa and 40-65MPa, respectively. Compared with low cement castables with good aluminum content and high strength, its thermal shock stability is better.
(2) With the slight expansion
Add a proper amount of expansion agent and materials containing aluminum and silicon into the castable. In order to produce micro expansion during use to prevent cracks.
(3) Good sintering performance
By adding an appropriate amount of sintering agent and other materials into the castable. During use at 1000~1350℃, the working layer of the wall can be sintered and formed into a whole. To adapt to its double-sided tropical working conditions.
For more information about refractories for regenerator heating furnaces, please visit our website: https://kilnrefractory.com/.