Difference between refractory mortar and refractory cement. The lining material of high-temperature industrial furnaces can be made of refractory bricks/wedges or by pouring refractory castables.
When the refractory brick or refractory wedge lining is installed, the bonding material between the pieces is mortar. The type of mortar selected must have characteristics quite similar to the material of the refractory brick used in the construction of the lining. Therefore, in Refractory Solutions, we, Rongsheng Kiln Refractory Company have mortars for all brick qualities. Refractory castables, on the other hand, need a binder to bind the raw materials together. The binder used in this case is generally refractory cement. This high alumina cement is mainly composed of calcium aluminate (CaO – Al2O3).
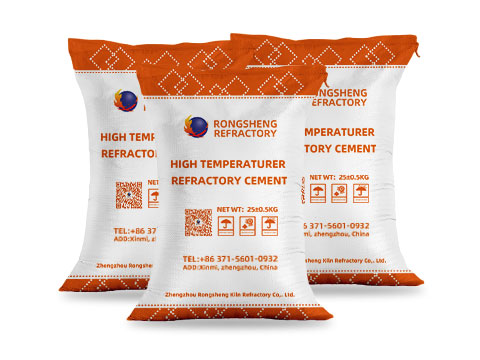
What are the differences between refractory mortar and refractory cement? In conclusion, the difference between refractory mortar and refractory cement is that mortar is used to join shaped materials and on the other hand, refractory cement is used as a binder material for refractory castables. In Refractory Solutions, RS Kiln Refractory Company, we advise you on any material need you may have. Contact us for free quotes or samples.
Refractory Cement: What it Is, Plus 3 Things You NEED to Know
In helping businesses and homeowners select the correct refractory product to use for their application a few common questions kept coming around about refractory mortar their uses. Because these questions are common to so many we speak with the following article is here to address the basics about refractory cement.
What is Refractory Cement?
Refractory Cement is a heat-resistant material designed to line fireboxes and withstand very hot environments (2,000-3,000*F) such as firebox linings, forges, kilns, ovens, incinerators, crematoriums, and other high temperature equipment. Refractory cement is commonly combined with other products like firebrick and other ceramics to further increase thermal resistance.
Keep reading to understand just how refractory cement also known as castable refractory or fire cement is used and how it differs from other similar products.
- What is Refractory Cement Made of?
Refractory cement is made from a combination of materials like calcined alumina, ganister/silicon carbide, zirconia, ceramic clay, and lime among other materials.
It is typically made from a mixture of refractory aggregates, bonding agents, and other materials that are designed to withstand high temperatures. The specific composition of refractory cement can vary depending on the intended use of the product,
These materials are chosen for their ability to withstand high temperatures and their low thermal expansion coefficients, which helps to prevent cracking or other damage to the cement. Refractory cement is often used in the construction of furnaces, kilns, and other high-temperature equipment, as well as in the manufacture of firebricks and other refractory products.
- Where is Refractory Cement Used?
Refractory cement is a high-temperature resistant material that is used in various industrial applications where it is subjected to extreme temperatures.
Some common uses of refractory cement include:
- Lining furnaces and kilns: Refractory cement is often used to line the inside walls of furnaces and kilns, where it helps to insulate the equipment and protect it from the high temperatures involved in the manufacturing process.
- Fireplace and wood stove construction: Refractory cement is used in the construction of fireboxes and wood stoves, where it helps to protect the structure from the high temperatures generated by the fire.
- Pizza Ovens: Wood fire pizza ovens typically include castable refractory cement in their construction.
- Boiler construction: Refractory cement is sometimes used in the construction of boilers, where it helps to insulate the equipment and protect it from the high temperatures and pressures involved in steam generation.
- Furnaces for Industrial Manufacturing: Refractory cement is used in the construction of furnaces, where it helps to insulate the equipment and protect it from the high temperatures involved.
- Crematoriums: The extreme temperatures required for the incineration of remains require refractory castables to help insulate and maintain hot operating temps.
- Other high-temperature applications: Refractory cement is also used in a variety of other high-temperature applications, such as in the manufacturing of ceramics, in the petrochemical industry, and in the production of iron and steel.
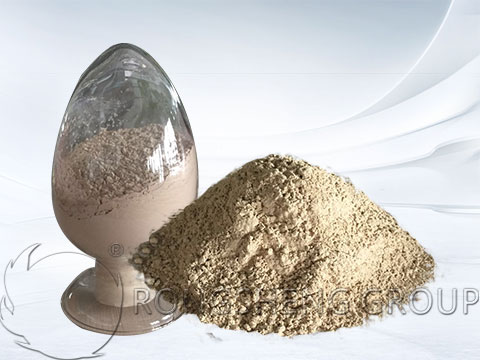
- Refractory Mortar vs. Refractory Cement, What’s the Difference?
Refractory cement and refractory mortar are both high-temperature resistant materials that are used in various industrial applications. However, there are some key differences between the two:
Composition: Refractory cement and refractory mortar are made from different materials and have different compositions. Refractory cement is typically made from a mixture of refractory aggregates, bonding agents, and other materials, while refractory mortar is made from a mixture of refractory cement and fine refractory aggregate.
Use: Refractory cement is typically used for constructing or repairing the structural elements of a furnace or other high-temperature equipment, while refractory mortar is used for filling in gaps and joints between refractory bricks or other masonry units.
Consistency: Refractory cement is typically thicker and more paste-like in consistency, while refractory mortar is thinner and more pourable.
Setting time: Refractory cement typically has a longer setting time than refractory mortar, which allows for more time to shape and form the material during construction.
Overall, the main difference between refractory cement and refractory mortar is in the intended use and application of the materials. Refractory cement is used for constructing or repairing the structural elements of a furnace or other high-temperature equipment, while refractory mortar is typically used for filling in gaps and joints between refractory bricks or other masonry units.
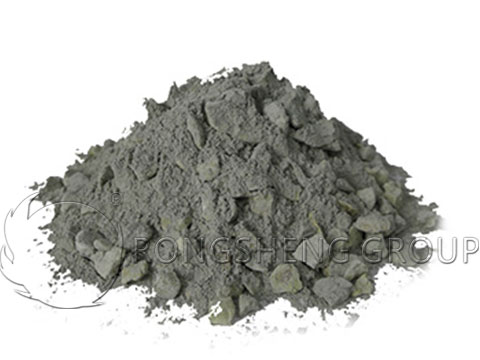
How Long Does It Take Refractory Cement to Cure?
Refractory cement manufacturers such as Rongsheng Kiln Refractory Company recommend at least 24 hours to cure before exposing it to high temperatures. The exact curing time for refractory cement depends on several factors, including the specific type of refractory cement being used, the ambient temperature and humidity, and the thickness of the cement layer. In general, refractory cement begins to harden within a few hours of being mixed and poured, and it can take anywhere from a few days to several weeks to fully cure.

What is Refractory Castable?
Refractory castable is a type of refractory material that is made from a mixture of refractory aggregate, bonding agents, and other additives. It is a type of refractory concrete that is used in various industrial applications where it is subjected to extreme temperatures. Refractory castable is typically poured into place and allowed to harden, rather than being molded or shaped like traditional concrete. It is often used in the construction or repair of furnaces, kilns, and other high-temperature equipment, as well as in the manufacture of firebricks and other refractory products.
Refractory castable has several advantages over other types of refractory materials. It is easy to install, can be poured into place, and can be shaped or formed to fit various applications. It is also relatively inexpensive compared to other types of refractory materials. However, refractory castable is not as strong as other types of refractory materials, and it may not be suitable for use in applications where high mechanical strength is required.
The 24 hour initial curing allows the cement to fully harden and achieve its maximum strength. In some cases, it may be necessary to allow the cement to cure for longer periods of time, particularly if the cement is being used in a high-temperature application or if it is being applied in a thick layer. It is important to follow the manufacturer’s recommendations for curing times to ensure that the cement is fully cured and ready for use.